2024.09.17
- 設備保全・補修
設備保全コンサルティング
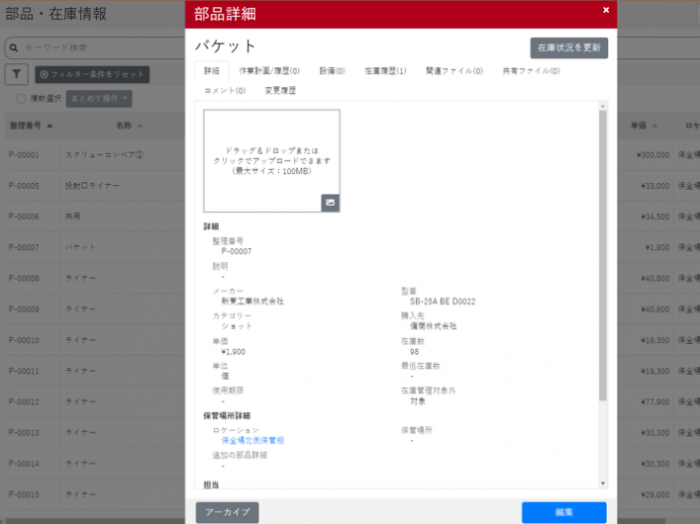
工場の稼働率と保全活動の重要性
工場の稼働率とは、工場の生産能力に対して実際にどれくらい生産できたのかを表す指標であり、「稼働率=実際の生産数÷生産能力」という計算で表します。製造業の工場で働く方にとっては、稼働率の向上は非常に重要な課題です。受注や在庫等との関係性から例外もありますが、一般的には稼働率=100%を目指すのが理想です。
しかし、実際にはなかなかうまくいかず、稼働率が下がってしまう要因は様々あります。そのうちのひとつが、設備の故障・停止です。工場内の設備やラインが停止すると、全体の生産が一時停止してしまいます。1時間停止するだけで1,000万円単位の損失が生じてしまうということもあります。そうならないためにも、設備の保全活動が非常に重要なのです。
工場の保全に関するよくある課題
しかし、保全活動を適切にできている工場は意外と少ないのが実情です。製造業全体の課題である「人手不足」「高齢化」などにより、工場設備の保全担当は不足しているケースが多いからです。
以下に、保全人員の不足による工場のよくある課題を列挙します。
◆ チョコ停が頻発する
◆ ちょっとした故障でラインが長時間停止してしまう
◆ 予防保全でなく事後保全になってしまい、コストが増大してしまう
◆ 保守部品がどこにあるのかわからない
◆ 保全人員の能力に偏りがあり、属人化している
◆ 保全スキルが向上する土台がない
◆ 図面を書類で管理している
3つの保全方法とその比較
保全の考え方は、事後保全と予防保全、予知保全の3つがあります。
それぞれの考え方は以下の通りです。
◆事後保全
壊れたらメンテナンス・交換する
壊れるまで使ってから設備を交換する
⇒あまり主要でない部品についてはこれで対応することが多い
◆予防保全
一定期間を決めて、メンテナンスを実施する
壊れていても壊れていなくてもメンテナンスを実施する
⇒設備台帳にて設備の経過年数を管理して行う
◆予知保全
設備の状況をセンシングして故障予兆を発見する
予兆を発見してからメンテナンスを実施する
⇒センサーやIoT機器を導入して行う
必ずしも事後保全が悪く、すべて予防保全や予知保全にした方がいい、というわけではありません。各設備や部品によってこれらをうまく使い分けるのが重要です。
しかし、重要な部品のため本来であれば予知保全・予防保全を行うべきなのに、事後保全となってしまい、結果として生産停止のロスなどで余計にコストがかかってしまうというケースが良くあります。予防保全・予知保全については定期的にコストがかかりますが、長期的に見ると予防保全の方が事後保全よりもコストを抑えられます。
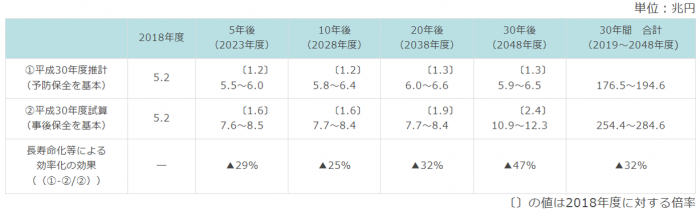
【事後保全と予防保全のコスト比較】
出典:国土交通省所管分野における維持管理・更新費の推計結果(H25.12)
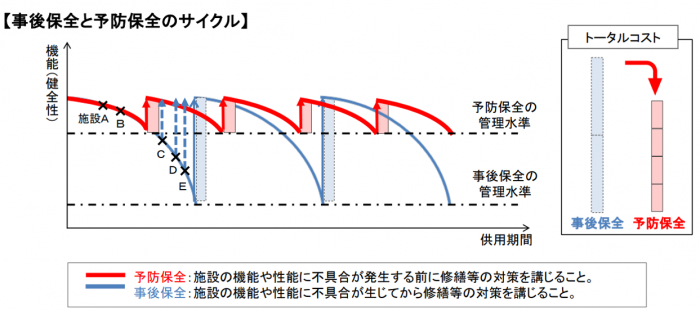
出典:国土交通省「公的ストックの適正化について(R1.10.11)」
設備保全クラウドサービスを活用した設備保全コンサルティング
弊社では、設備保全に特化したクラウドサービス「MENTENA」を活用し、お客様の設備保全を定期的に行う設備保全コンサルティングを行っています。
「MENTENA」の詳細はコチラ
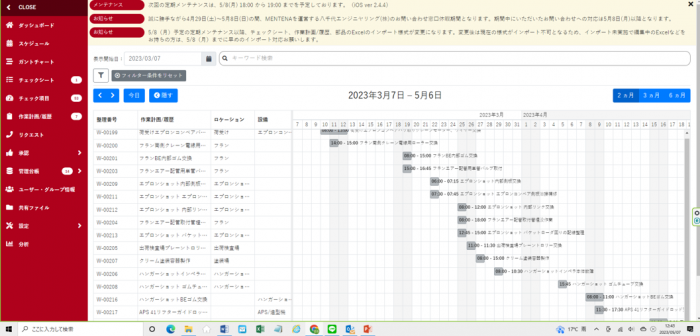
お客様にて行っていた保全情報の管理を代行し、さらにそこに蓄積したデータをもとに定期的なメンテナンス、保全計画の立案、アドバイスを行います。
【コンサルティング内容】
お客様の工場に弊社のスタッフが月2回(平日1回、休日1回)訪問し、保全情報の管理や点検・メンテナンスを行います。クラウドサービスを活用して遠隔で監視することができるため、工場常駐と比較して保全コストを抑えることが大きなメリットです。
◆平日点検
・電気図面の管理&データ化
・MENTENAの入力
・稼働中の設備状態の点検
・保守部品の管理
・改善計画の立案&指導
・保全担当とのミーティング
◆休日点検
・設備を停止した際の入念な設備&盤点検
・PLC、タッチパネル、インバータデータのバックアップ
・絶縁物、盤内清掃
・端子増し締め
・不良箇所の補修&部品交換
◆主な効果・メリット
・保全活動の効率化&省人化
・最適な設備投資の計画策定が可能
・工場稼働率の向上
・人手不足の解消
・保全スタッフの教育
なお、保全内容はお客様のご要望に合わせて柔軟に対応いたします。
サイテックの設備保全コンサルティングの強み
1.回路設計を伴うメンテナンスも一括対応
機器の交換などを行う際、場合によっては回路設計から行う必要があります。
私たちは、回路図を設計することができるスタッフが在籍しているため、そのような場合でも自社ですべて対応することができます。
そのため、「回路設計を伴う部分については他の業者に依頼する」というような手間を削減することができます。
2.故障の要因となる電気的トラブルについても、原因特定が可能
機械の故障の要因は、大きく機械的トラブル(部品の劣化等)と電気的トラブル(回路の不具合等)に分かれます。
簡易的な設備保全の場合、機械的な故障要因のみ特定する場合がありますが、電気的な問題も存在する場合、根本解決にはなりません。
私たちは、まずは電気的なトラブルが無いかを確認したうえで、機械的なトラブルを特定します。
そのため、確実にトラブルの要因を特定し、補修することができます。
ご興味のある方は、お気軽にご相談ください。